Estendere Internet alle cose è stato per anni uno dei punti su cui la ricerca industriale ha lavorato maggiormente. La rilevazione dei dati si basa sull’utilizzo di sensori, o sulla generazione di valori logici da parte di unità di controllo (in ambito industriale pensiamo ai PLC, o ai controlli numerici), mentre per la trasmissione e la condivisione sono disponibili svariati protocolli e architetture di riferimento (framework). Sempre più spesso ci accorgiamo di quanto i dati siano una parte fondamentale delle nostre attività quotidiane: monitoriamo l’ossigenazione del sangue dallo smartwatch, tracciamo i nostri pacchi dal telefono, e possiamo accendere il riscaldamento di casa sapendo a priori che farà freddo. E se anche con i dati di produzione potessimo fare cose simili? Quali parametri e con quali modalità potremmo alimentare applicazioni intelligenti per migliorare un’attività produttiva? Per rispondere a queste domande dobbiamo partire dalla consapevolezza che i dati, oggi, rappresentano una preziosa risorsa nelle fabbriche connesse.
Indice degli argomenti
La spinta di Industria 4.0
L’avvento dei vari piani nazionali “Industria 4.0” [1], poi “Impresa 4.0” [2] e ora “Transizione 4.0” [3] hanno spinto le aziende manifatturiere italiane verso la digitalizzazione dei processi produttivi. Tutte le normative susseguite fino a oggi hanno incluso l’interconnessione dei beni come requisito fondante [4], sottolineando la necessità di utilizzare protocolli documentati e standard per favorire l’integrazione dei dati con sistemi terzi.
Terzi, ovvero sistemi non necessariamente afferenti al contesto produttivo in cui macchine utensili, e più in generale le tecnologie di produzione, hanno operatività. Sebbene infatti la summa dell’integrazione manifatturiera era spesso rimasta ancorata al solo concetto di CAD/CAM, i recenti sviluppi tecnologici hanno scoperchiato il vaso di Pandora delle tecnologie IT (Information Technologies) applicate ai processi produttivi.
Le imprese si sono quindi trovate tempestate di nuovi termini, che seppur presenti anche in anni precedenti, acquisivano ora la spinta favorevole del treno di Industria 4.0. Data analytics, manutenzione predittiva, monitoraggio energetico, MES, ERP, teleservice, adattività, digital twin, cybersecurity, e si potrebbe andare avanti con ulteriori scrosciate di applicazioni.
Il rischio, corso purtroppo da molte aziende che tutt’ora faticano ad adottare questi nuovi strumenti [6] è quello di rimanere indietro, perdendo il treno dell’innovazione.
Cerchiamo di fare chiarezza per orientarsi tra queste applicazioni, identificando innanzitutto quali e quanti dati abbia senso recuperare. A partire dall’Internet of Things [7].
Sensori, protocolli di connessione, sistemi per la gestione dei dati
Estendere Internet alle cose è stato per anni uno dei punti su cui la ricerca industriale ha lavorato maggiormente. E non pensiamo ad applicazioni utili solamente a scienziati in camice bianco; pensiamo ad esempio al modo in cui oggi controlliamo le nostre attività sportive monitorando percorsi e prestazioni. Oppure proviamo a ricordarci l’ultima volta in cui abbiamo guardato il libretto dell’auto per capire quanto mancava al prossimo tagliando, invece che aspettare il messaggio automatico della centralina. Tutte queste applicazioni si basano sul concetto di Internet of Things (IoT), ovvero l’idea di estendere la connettività anche a oggetti, luoghi e processi di tutti i giorni. La base di questo è un insieme di oggetti in grado di sentire, trasmettere e condividere dati, collegati tra loro su reti pubbliche o private.
La rilevazione di questi dati si basa sull’utilizzo di sensori, o sulla generazione di valori logici da parte di unità di controllo (in ambito industriale pensiamo ai PLC, o ai controlli numerici), mentre per la trasmissione e la condivisione sono disponibili svariati protocolli e architetture di riferimento (framework).
Sono quindi tre gli attori principali in questa trasformazione:
- Sensori, per la rilevazione di grandezze dal campo;
- Protocolli di connessione, che invece definiscono regole di trasmissione;
- Sistemi per la gestione e il consumo dei dati.
Ognuna di queste voci gode di un capitolo a sé stante nel dizionario di Industria 4.0, ma per un primo approccio ci basterà sapere che più di qualsiasi altra cosa, quello che ci dovrà portare a scegliere un tipo di sensore, piuttosto che un protocollo specifico o una piattaforma gestionale, dovrà essere il risultato atteso alla fine di tutte le elaborazioni. Deve essere chiaro in fase di progettazione quale sia lo scopo ultimo delle analisi che andremo a fare, perché il dato non ha alcun utilizzo se non viene consumato. Salire nella catena alimentare dei dati [8], trasformandosi prima in informazione, poi in conoscenza, richiede l’introduzione dell’ultimo elemento: il sistema cyberfisico (CPS) [9].
Fabbriche smart e connesse
In ambito industriale il concetto di Internet of Things si rafforza ulteriormente e prende il nome di Industrial Internet of Things (IIoT). Il cardine è sempre la connessione tra dispositivi, ma in questo caso consideriamo macchinari, ordini di produzione, utensili e tutto ciò che ha a che fare con l’ambiente produttivo.
Un’applicazione pratica di questo concetto la ritroviamo nei sistemi di monitoraggio, che sfruttano i dati esposti dalle attrezzature per analizzarli e riformattare in metriche più digeribili e immediate, esposte tramite dashboard o pannelli di controllo. Altri usi possono riguardare il contributo in fase di progettazione, la gestione delle risorse e il supporto alla pianificazione.
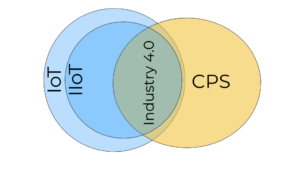
Fig.1 – Visualizzazione dell’interazione tra IoT, CPS, IIoT, da [10]
L’immagine riportata in figura aiuta nel comprendere la relazione tra Internet of Things e applicazioni 4.0, e possiamo ora introdurre i sistemi cyberfisici (CPS). Questi sono sistemi di calcolo, interconnessi tra di loro e con il mondo fisico circostante, in grado di sfruttare servizi condivisi di accesso e gestione dei dati nelle fabbriche connesse.
Riportiamo la definizione in termini industriali: il dato, reso disponibile tramite l’IIoT, viene consumato da un’applicazione finale. Questa lo userà per generare una nuova interazione con il processo, come per esempio attivare un determinato sottosistema della macchina utensile per compensare una variazione di processo (adattività alle derive). Oppure potrebbe elaborare una metrica di efficienza di impianto comparando la qualità finale di un prodotto con le ore di produzione rispetto alle ore di possibile produzione (OEE). E potremmo anche spingerci a immaginare un sistema di fabbrica che auto regoli la propria produzione in funzione della quantità di materiali grezzi e consumabili disponibili nei nostri magazzini.
Potremmo andare avanti per molto con esempi di questo tipo, ma ci limiteremo a condensare l’importanza di questa struttura nella creazione di nuove applicazioni e livelli di servizio
Fabbriche connesse, la centralità del dato
Ma veramente queste sono nuove applicazioni? Ovviamente no. Il sogno di una fabbrica connessa era già nei sonni inquieti dei tecnici che per primi avvicinarono l’idea di un calcolatore alle macchine di produzione, e nel corso degli anni abbiamo trovato vari modi per riferirci a questo concetto [11]. Senza andare troppo lontano ci basti pensare che già nel 1988 ad Erba si presentavano impianti produttivi interoperabili tra diverse tecnologie, in grado di sfruttare l’intelligenza artificiale per ottimizzare la produzione [12].
Cosa è cambiato quindi da allora?
In breve:
- La potenza di calcolo è salita di ordini di grandezza rispetto agli anni in cui questi concetti venivano formulati. Ora i controlli numerici hanno velocità così spinte da consentire reazioni quasi istantanee nel processo produttivo, abilitando quindi controlli ad anello chiuso anche per i processi più complessi.
- I dati a cui possiamo accedere sono più robusti, grazie allo sviluppo di protocolli resilienti e condivisi. Le richieste di produzione passano attraverso mail, database gestionali, e possiamo tracciare e registrare più facilmente le variabili di controllo nei processi industriali.
- Scrivere un’applicazione richiede qualche ora di impegno davanti ad un tutorial, e sono disponibili ambienti di programmazione completamente gratuiti ed open source, per diventare in breve tempo programmatori in grado di sviluppare software per l’industria.
Se oggi la disponibilità di hardware pare scontata, così come la possibilità di scrivere “Hello World” su un qualsiasi controllo numerico [13], non è così facile districarsi tra gli svariati protocolli e framework disponibili per rendere efficienti e puntuali queste soluzioni. Resta ancora una difficoltà tecnica nella selezione dei dati, un savoir-faire proprio di quelle figure che riescono a miscelare correttamente competenze IT alla conoscenza dei processi industriali.
Ritorniamo quindi al punto di partenza: la centralità del dato. L’importanza di sapere quale misurazione sia rappresentativa per il processo che vogliamo studiare si lega alla selezione del metodo più efficiente per trasferirla nei nostri sistemi informatici. La strada verso industrie connesse ed intelligenti è ora accessibile a tutti i naviganti dotati di una bussola, ovunque punti.
Riferimenti
[1] Ministero dello Sviluppo Economico, Italy’s Plan Industria 4.0, (2017)
[2] Ministero dello Sviluppo Economico, Italy’s Plan Impresa 4.0 (2018) https://www.mise.gov.it/images/stories/documenti/investimenti_impresa_40_ita.pdf
[3] Ministero dello Sviluppo Economico, Italy’s Plan Impresa 4.0 (2020) https://www.mise.gov.it/images/stories/documenti/Slide_transizione40-maggio2020.pdf
[4] Gazzetta Ufficiale della Repubblica Italiana (2016) Legge 11 dicembre 2016, n. 232 https://www.gazzettaufficiale.it/eli/id/2016/12/21/16G00242/sg
[5] Agenzia delle Entrate, Circolare N.4/E del 30/03/2017
https://www.mise.gov.it/images/stories/normativa/Circolare_Agenzia_entrate.pdf
[6] A. Rangone, The Techno–Corporate Gap in Italy: Critical Factors and Possible Solutions, in: Manag. Corp. Innov. Contrib. to Manag. Sci., Springer, 2020. https://doi.org/10.1007/978-3-030-31768-3_9.
[7] M. Rüßmann, M. Lorenz, P. Gerbert, M. Waldner, J. Justus, P. Engel, Michael Harnisch, Industry 4.0 – The Future of Productivity and Growth in Manufacturing Industries, Bost. Consult. Gr. Rep. (2015).
.
[8] Rowley, Jennifer (2007). “The wisdom hierarchy: representations of the DIKW hierarchy”. Journal of Information and Communication Science. 33 (2): 163–180. doi:10.1177/0165551506070706
[9] A.A. Letichevsky, O.O. Letychevskyi, V.G. Skobelev, V.A. Volkov, Cyber-Physical Systems, Cybern.Syst. Anal. 53 (2017) 821–834. https://doi.org/10.1007/s10559-017-9984-9.
[10] E. Sisinni, A. Saifullah, S. Han, U. Jennehag, M. Gidlund, Industrial internet of things: Challenges, opportunities, and directions, IEEE Trans. Ind. Informatics. 14 (2018) 4724–4734. https://doi.org/10.1109/TII.2018.2852491.
[11] B. Sniderman, M. Mahto, M.J. Cotteleer, Exploring the world of connected Enterprises, Industry 4.0 and manufacturing ecosystems, February 2016
[12] E.L.M.E.P.E. – Tèchne 88
https://drive.google.com/file/d/1P8bTCKgwNil0hxaU2SgmIMrY9gTGvJ1K/view?usp=sharing
[13] Linux CNC
http://linuxcnc.org/