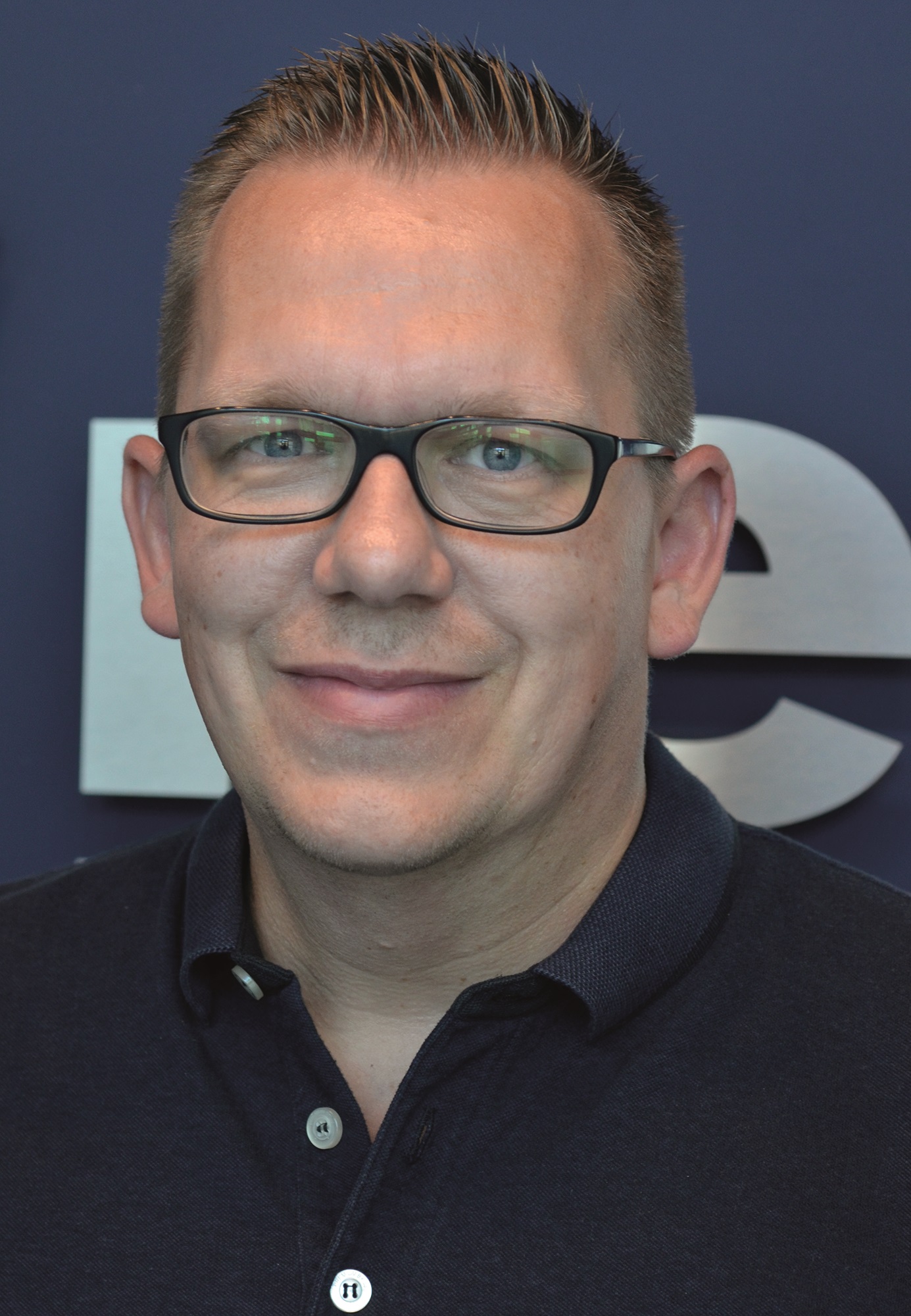
Il processo di trasformazione digitale del mondo industriale verso il concetto di Industria 4.0 non deve essere percepito come un salto nel vuoto legato necessariamente all’intera sostituzione dei macchinari in uso. Al contrario, infatti, i risultati di digitalizzazione migliori e più sostenibili nel tempo possono essere raggiunti con una politica di piccoli passi e delineata da un percorso graduale.
Il concetto di Industria 4.0 fa leva su una produzione in grado di adattarsi in modo agile e dinamico ad uno scenario in continuo cambiamento e di evolversi rapidamente per rispondere alle mutevoli esigenze. Per cavalcare questa tendenza, grandi volumi di dati devono essere continuamente raccolti sia all’interno sia tra i singoli macchinari e successivamente comunicati all’intero ecosistema per essere valutati nei vari livelli di tecnologie operative (OT) e tecnologie dell’informazione e della comunicazione (ICT).
Le opportunità legate alla capacità di raccogliere e valutare quantità sempre maggiori di dati riguardano la digitalizzazione di tutti i processi aziendali e produttivi, la creazione di valore industriale, le operazioni di funzionamento e manutenzione degli impianti per una maggiore efficienza e affidabilità, oltre che lo sviluppo di modelli di business completamente nuovi. I dati rappresentano il primo step per attuare una trasformazione digitale in modo agile e automatizzato: un processo che richiede, tuttavia, un collegamento in rete di tutte le macchine e degli impianti, nonché di sensori e attuatori aggiuntivi estesi a tutte le sedi di un’azienda. Un metodo espresso sotto il concetto di Industrial Internet of Things (IIoT).
Indice degli argomenti
Valutazione della situazione attuale
In occasione di Hannover Messe 2011 fu proclamato l’inizio della quarta rivoluzione industriale. Secondo uno studio sul grado di implementazione dell’IoT nel settore industriale condotto nel 2019 da IDC – società di ricerca del mercato IT -, gli impianti auto-ottimizzanti sono ancora una rara eccezione. Infatti, assistiamo spesso a interruzioni di sistema ostruttive tra le singole parti degli impianti di produzione, in cui raramente l’IIoT è usato come hub per le informazioni.
Ciò nonostante, secondo l’indagine condotta da reichelt elektronik nel mese di settembre 2020, circa il 26% delle aziende italiane stava pianificando investimenti per l’espansione dell’IIoT nel prossimo futuro. Tra i principali settori che hanno affermato di voler cavalcare questa tendenza, emergono soprattutto l’industria di produzione, la logistica e l’intera catena di approvvigionamento e smaltimento, in cui la maggior parte dei decision maker riconosce il ruolo dell’IIoT quale abilitatore della trasformazione digitale. Sebbene i macchinari, l’hardware di controllo e il software impieghino diversi decenni per crescere ed ampliarsi organicamente, la digitalizzazione end-to-end della produzione non è quasi mai legata ad una sostituzione completa dei sistemi o anche dei singoli macchinari.
Adattare le tecnologie in uso
La buona notizia è che le macchine e i sistemi possono essere gradualmente trasformati in oggetti cyber-fisici attraverso il retrofit e integrati nell’IIoT, purché dispongano di sistemi informatici e di controllo appropriati, e possono essere dotati di concetti operativi moderni e integrati, oltre ad un maggior livello di automazione. In questo contesto, il cablaggio e il collegamento in rete degli impianti esistenti nel cosiddetto brownfield (in contrapposizione ai nuovi impianti greenfield), così come la necessaria tecnologia dei sensori aggiuntivi, consentono agli ingegneri dedicati all’automazione degli impianti di affrontare sfide sempre più complesse.
Ovviamente è indispensabile che ogni caso sia adattato alle diverse esigenze e in grado di rispondere alle specifiche necessità dell’impianto, ma rivedere l’intero assetto industriale in un’ottica di modernizzazione e adattarlo all’IIoT attraverso l’informatizzazione è una strategia vincente e orientata al futuro.
Creare modularità e indipendenza
L’arte sta nell’utilizzare le possibilità esistenti liberamente nei vari punti dell’intera rete per adattarle al meglio alle esigenze del luogo, oltre che nel creare una intera rete inevitabilmente eterogenea come un kit di costruzione modulare flessibile di unità autonome. A tal fine, è bene conoscere le diverse possibilità tecniche per collegare in rete i sensori e gli attuatori, sia quelli esistenti che quelli aggiunti successivamente nelle macchine, con i relativi sistemi di controllo, i sistemi secondari e i sistemi superiori (sistemi dei sistemi).
Una scelta agnostica della tecnologia e dei prodotti può evitare un’eccessiva dipendenza dagli standard dei singoli produttori di hardware e garantire un alto livello di efficacia dei costi nel funzionamento e nella manutenzione. L’attenzione principale riguarda la connettività ai vari livelli di tecnologia dei dati.
Reti per il trasporto dei dati
Anche quando si sceglie il supporto fisico per i dati, ci si trova di fronte ad un’enorme varietà e si tenderà probabilmente a fare affidamento su cavi industriali in rame – i connettori M12 ne sono un esempio – e, solo in casi a rischio interferenza, su cavi in fibra ottica. Per la comunicazione esterna, invece, la tendenza è sempre più spesso quella di fare appello ad una connessione WLAN o ad altre reti di trasmissione via radio, a causa del cablaggio spesso difficile e costoso negli impianti di produzione esistenti.
Tra le modalità di connessione vi è anche l’imminente standard di comunicazione mobile 5G, anche se la sua idoneità per il trasporto dei dati nell’IIoT è ancora al centro del dibattito pubblico. Numerosi produttori mettono continuamente sul mercato dispositivi di interfaccia adatti, ma il trasporto dei dati tramite 5G si rifletterà chiaramente nel costo del funzionamento del sistema.
In alternativa, le reti di trasmissione sviluppate appositamente per l’IIoT possono essere utilizzate per consentire ai sensori di comunicare direttamente con l’IT, bypassando i sistemi di controllo esistenti. Queste includono la rete wireless globale Sigfox o la Long Range Wide Area Network (LoRaWAN). I sensori LoRaWAN sono i più scelti per i loro requisiti di alimentazione particolarmente bassi ed una sicurezza intrinseca dei dati molto elevata, elementi che li rendono particolarmente adatti all’integrazione di sistemi remoti e persino mobili.
Integrare o bypassare i sistemi esistenti?
I dati e i segnali aggiuntivi dai sensori montati a posteriori non sono solo rilevanti per i sistemi di livello superiore, ma anche per i sistemi locali di controllo, regolazione e visualizzazione. La connessione a tali sistemi è solitamente stabilita tramite moduli I/O compatibili con il bus di campo esistente o con la rete Ethernet industriale. In questo contesto, la selezione dei componenti è significativamente influenzata dalle versioni per il montaggio su guida DIN nell’armadio di comando esistente o un armadio di comando aggiunto secondo le necessità. Nei casi in cui la situazione sia differente, è indispensabile la disponibilità di varianti in classi di protezione più elevate e con una gamma di temperatura estesa, nonché con l’opzione di alimentazione tramite bassissima tensione per il montaggio direttamente sul telaio della macchina.
Spesso, i controllori di macchine esistenti non hanno libertà di decisione. Pertanto, i produttori di soluzioni IIoT devono aggiungere un altro livello di elaborazione. Un’intelligenza computazionale locale si occupa della pre-elaborazione e della traduzione delle informazioni aggiuntive, della comunicazione con l’unità di controllo esistente e dell’inoltro dei dati all’esterno. In questo processo, le versioni industriali del Raspberry Pi, un piccolo computer che può essere programmato in modo flessibile, stanno prendendo piede a discapito dei dispositivi PLC che hanno dominato in passato.
Tutto da un’unica fonte
Sia che si continui a usare la struttura di rete esistente, che si introduca una rete basata sulla radio o che si stabilisca una connessione diretta ai servizi cloud (o qualsiasi combinazione tra queste), gli elementi centrali dell’aggiornamento della connettività sono gli switch, i router e i convertitori di protocollo. Come tutti gli altri componenti, dai gruppi di cavi agli scaricatori di sovratensione, questi non devono essere disponibili solo nelle versioni industriali.
I progetti IIoT sono molto individuali, i loro creatori installano componenti e dispositivi in quantità molto piccole, fino al singolo pezzo. È necessario fornire loro l’hardware richiesto con le proprietà di compatibilità appropriate con breve preavviso, anche in piccole quantità e con riproducibilità a lungo termine da un’unica fonte.
Didascalie immagini
- Rendere le macchine industriali esistenti nel cosiddetto brownfield adatte all’IIoT, dotarle di concetti operativi aggiornati e integrati e aumentare il loro grado di automazione è una sfida complessa gli ingegneri che si occupano di automazione degli impianti.
- Oltre ai sensori aggiuntivi, i produttori di soluzioni IIoT richiedono anche sistemi I/O, sistemi di controllo e computer di bordo, comprese le connessioni in cloud. La selezione di componenti industriali adatti e della connettività appropriata per il caso di applicazione specifico è essenziale per la costruzione di un ecosistema efficiente e modulare.