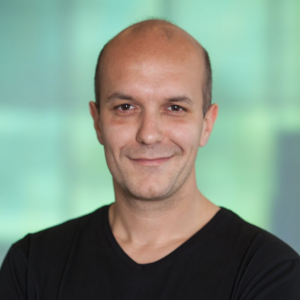
Internet of Things, Analytics, Cloud, Machine Learning, automazione, robotica e robotica collaborativa: il profilo dei “fattori abilitanti” per l’Industria 4.0 appare sempre più chiaro, ma se si deve identificare il vero asset sul quale si sviluppano le possibilità di crescita dell’Industria 4.0, si deve guardare agli Skill. E’ la convinzione di Roberto Andreoli, Direttore della Divisione Cloud & Enterprise di Microsoft Italia che sottolinea come l’Industria 4.0 e il digitale per il mondo del manufacturing e della fabbrica ha prima di tutto bisogno di competenze adeguate. «Fare Industria 4.0 oggi vuol dire sviluppare skill digitali che siano in grado di sfruttare al massimo la capacità di generazione di dati che arriva dall’IoT e di trasformazione di questi dati in conoscenza e in azioni che è oggi percorribile grazie al Cloud».
E per chiarire ancora meglio la propria visione dell’Industria 4.0, Andreoli invita a considerare che questa sfida nelle non è oggi tanto sulla tecnologia. «La tecnologia – precisa – è oggi certamente molto più accessibile di quanto non fosse nel passato. Il valore aggiunto per le imprese è nella capacità di utilizzarla al meglio, in funzione degli obiettivi che ciascuna azienda si pone e di sfruttare la situazione contingente favorevole, ad esempio, in questo periodo grazie anche alle condizioni che arrivano dagli incentivi agli investimenti del Piano nazionale Industria 4.0 (Piano Calenda).
Indice degli argomenti
Il rapporto tra Cloud e Internet of Things
E a proposito di accessibilità delle tecnologie Andreoli osserva che il Cloud permette alle imprese di fare innovazione disponendo di una migliore visione d’insieme dei valori dell’impresa e soprattutto, permette alle aziende di fare innovazione in modo graduale e “preciso”. Con la possibilità di disegnare delle roadmap che sono funzionali agli obiettivi e ovviamente ai budget e che magari possono anche prevedere la necessità di fare sperimentazione. Con il Cloud le aziende possono testare, possono eventualmente “sbagliare“, che è comunque un fattore importante di conoscenza e possono aggiustare il percorso in corso d’opera, più velocemente di quanto non fosse possibile in passato e senza dover fare tutto in “casa”.
Andreoli, che guida il team Microsoft dedicato all’innovazione dell’IT nelle imprese con l’obiettivo di diffondere l’utilizzo del Cloud Computing, dell’IoT e della Business Intelligence, rileva poi che non è “solo” il Piano Calenda a creare un contesto complessivamente più favorevole all’innovazione. L’evoluzione tecnologia a sua volta ha contribuito ad abbassare le barriere di accesso. E i fattori che abilitano l’Industria 4.0, come osserva Andreoli, sono fondamentalmente due: da una parte la riduzione dei costi dei sensori che sono più accessibili, e nello stesso tempo più performanti e permettono di disporre di maggiori quantità di dati, in modo più veloce e preciso. Il secondo grande fattore che abilita l’Industria 4.0 (e altri fenomeni, come ad esempio il digital banking, il digital finance) è la risposta al tema della crescita e della elaborazione dei dati. «Oggi sappiamo dove “mettere” l’enorme quantità di dati che arriva dall’IoT – afferma Andreoli – e sappiamo come leggerli, analizzarli e usarli in modo facile, scalabile e flessibile».
Il Cloud per l’Industria 4.0
La risposta è nel Cloud. «Con il Cloud le aziende possono disporre di una capacità potenzialmente infinità di “archiviazione” e di una altrettanto (potenzialmente) infinita capacità di calcolo, cui si aggiungono le opportunità di “dare in pasto” questi dati, ad esempio, a soluzioni di Machine Learning che aumentano esponenzialmente la capacità di estrarre conoscenza dai dati stessi».
Ma Andreoli aggiunge un altro aspetto importante che riguarda il tema dell’accessibilità: «Con il Cloud anche le aziende di dimensioni medio piccole hanno la possibilità di disporre di risorse un tempo inaccessibili in ragione dei costi e possono scalare, in modo graduale, l’utilizzo di queste risorse. In altre parole ci sono oggi le condizioni per fare progetti importanti di Industria 4.0 anche per aziende di piccole dimensioni.
Ma non è solo una questione di “costi” c’è anche una grande questione di soluzioni e di capacità di accompagnare le aziende verso l’Industria 4.0 o verso l’adozione di soluzioni in grado di sfruttare le potenzialità dell’IoT ed è qui che entra in gioco l’ecosistema dei partner e degli ISV Microsoft. «L’Industria 4.0 si affronta in team e Microsoft conta su una rete di oltre 35 mila partner a vari livelli, con una fittissima presenza sul territorio».
Il Ruolo di IoT Central: focus su Interoperabilità
Ma soprattutto nell’Internet of Things c’è una grande necessità di mettere “in ordine” le logiche di sviluppo e l’organizzazione degli apparati, dei device, delle fonti e dei dati. Ed è qui che è arrivata la piattaforma IoT Central che Microsoft ha lanciato recentemente e che si pone l’obiettivo di dare vita al “gestionale” dell’Internet of Things. Una piattaforma che ha lo scopo di accelerare lo sviluppo di soluzioni e di applicazioni e di offrire maggiori garanzie di interoperabilità. (Per saperne di più su IoT Central)
La logica IoT Central si innesta nel lavoro legato al programma di certificazione Azure IoT Certified un programma di certificazione dell’hardware che consente di garantire i parametri di trasferimento dei dati in modo sicuro. IoT Central e Azure IoT Certified si agganciano a un altro passaggio importante per Microsoft particolarmente significativo nel mondo dell’Industria 4.0 vale a dire IoT Edge. «Sono tanti i contesti nei quali è necessario portare la capacità di calcolo esattamente dove serve. Non tutti i dati che arrivano dall’IoT devono essere portati sul Cloud, in tanti casi possono rappresentare un inutile appesantimento delle reti e dei sistemi e costituiscono un costo. E’ necessario disporre di capacità computazionale a livello locale e serve predisporre delle soluzioni in grado di portare dei livelli di funzionalità Azure IoT anche all’interno della fabbrica, per ottimizzare il trasferimento preciso dei dati che è effettivamente necessario trasferire, e per elaborare a livello locale i dati che sensatamente devono compiere il loro lavoro a “livello locale” e non ultimo per gestire il lavoro anche nei momenti di disconnessione».
La Predictive Maintenance di Tenova
Ma L’Industria 4.0 ha prima di tutto bisogno di parlare attraverso case history che permettano di dimostrare concretamente cosa si può fare e che risultati si possono raggiungere.
«Con il caso Tenova (azienda del gruppo Techint) – racconta Andreoli – siamo perfettamente in ambito Industria 4.0. Tenova opera nell’ambito della produzione con attività nel siderurgico e nel manifatturiero e in questo caso si è portata intelligenza negli stabilimenti per avere più efficienza, più sicurezza e più leve per l’evoluzione del business».
Il primo grande tema di questo caso come di tanti altri casi legati all’Industria 4.0 è quello che riguarda «la capacità di tradurre il dato in informazione. Questo è il nostro focus ed è il nostro mestiere – precisa -. Non ci sostituiamo a chi fa sensoristica. Come Microsoft lavoriamo sui dati che arrivano dai sensori per gestire i flussi, per analizzare i dati stessi, per selezionarli e per trasformarli in azioni collegate al business».
Tenova ha predisposto una rete di sensori e rilevatori e da qui è partita con un progetto costruito su tre pillar:
- la base di rilevazione IoT
- lo sviluppo di intelligenza decentralizzata
- la creazione di servizi che permettono la interazione tra cliente e fornitore
Uno degli obiettivi del progetto è nella Predictive Maintenance e si pone l’obiettivo di aumentare l’efficienza della produzione riducendo al massimo i fermi macchina e gli errori. Grazie all’Internet of Things nella forma di sensori e di attuatori la soluzione è in grado di rilevare una ricchissima serie di dati e informazioni sullo stato di salute degli impianti e sullo svolgimento delle attività di produzione. Su questi dati entra appunto in gioco Microsoft con l‘intelligenza artificiale decentrata che lavorando sulle informazioni raccolte, sullo storico dei comportamenti e delle situazioni permette di determinare delle azioni conseguenti a determinati eventi e di sviluppare forme di manutenzione predittiva. In corrispondenza della rilevazione di segnali legati al comportamento delle macchine “fuori norma” gli operatori possono predisporre azioni manutentive che anticipano i possibili guasti, ovvero il sistema stesso può predisporre in automatico interventi che permettono di trasferire la produzione su altre macchine evitando il rischio di interruzione della produzione.
L’intelligenza artificiale decentrata si concretizza grazie alla connessione tra le fonti di dati rappresentati da sensori IoT presenti sulle macchine e sugli impianti produttivi e il Cloud Azure, dove le applicazioni basate su algoritmi previsionali di Machine Learning permettono di analizzare il funzionamento delle macchine in circostanze sempre diverse e permettono di raggiungere una configurazione ottimale dell’impianto.
Industria 4.0 come sicurezza e sostenibilità
L’altro grande obiettivo di questo progetto per Tenova riguarda i temi della sicurezza e della sostenibilità ambientale. I dati che servono per la Predictive Maintenance sono alla base di informazioni permettono di disporre di dati anche sugli ambienti di produzione e di aumentare il livello di sicurezza e il rispetto ambientale. In assoluto i KPI di questo tipo di investimenti Industry 4.0 possono essere misurati in OEE (Overall Equipment Efficiency) ovvero nell’incremento dell’indice di efficienza totale dell’impianto industriale in parallelo con una riduzione dei consumi energetici. Ultimo, ma certamente non meno importante, la possibilità di disporre di queste quantità di dati consegna agli operatori una visione molto più completa di tutti i componenti degli impianti e del loro comportamento e permette di controllare in modo più preciso le prestazioni di ogni singolo componente.
La collaborazione con la Factory 4.0 McKinsey di Pordenone
Un altro grande tema per l’industria 4.0 è dato dall’impegno nella ricerca, nello sviluppo di competenze e nella condivisione e divulgazione di queste competenze. Andreoli richiama la collaborazione di Microsoft con McKinsey e altri partner nell’esperienza della Factory 4.0 di Pordenone dove è stata ricreata una catena produttiva alla quale sono state applicatere tecnologie digitali nell’ottica Fabbrica 4.0. Il progetto si pone l’obiettivo di mettere a disposizione delle aziende la possibilità di testare e vedere all’opera le soluzioni di Intelligenza Artificiale Microsoft per sperimentare e verifiare nuove forme di collaboration, per valutare l’efficienza di nuovi modelli e per impostare logiche di servizio sulla manutenzione predittiva attraverso l’uso di Internet of Things e Machine Learning. Ma il centro, che si inserisce nel network globale dei Digital Capability Center di McKinsey, ha anche lo scopo di analizzare nuovi modelli a livello di cooperazione uomo-macchina, con lo studio di Interfacce, di linguaggi naturali basate su voce, gesti e studio dei comportamenti.